- Home
- Industries
- Metal tools
Metal tools
The metal tooling industry manufactures tools used in machining, forming, cutting, and assembly operations. This includes drills, dies, molds, punches, saw blades, cutters, chisels, reamers, and inserts made from tool steels, carbides, and specialty alloys. These tools face extreme conditions including high friction, impact, and heat, which means they must be hard, wear-resistant, and precisely shaped.
The industry relies heavily on heat treatment processes like hardening, tempering, and annealing to ensure long tool life and performance. In these areas, induction heating offers distinct control, efficiency, and speed advantages.
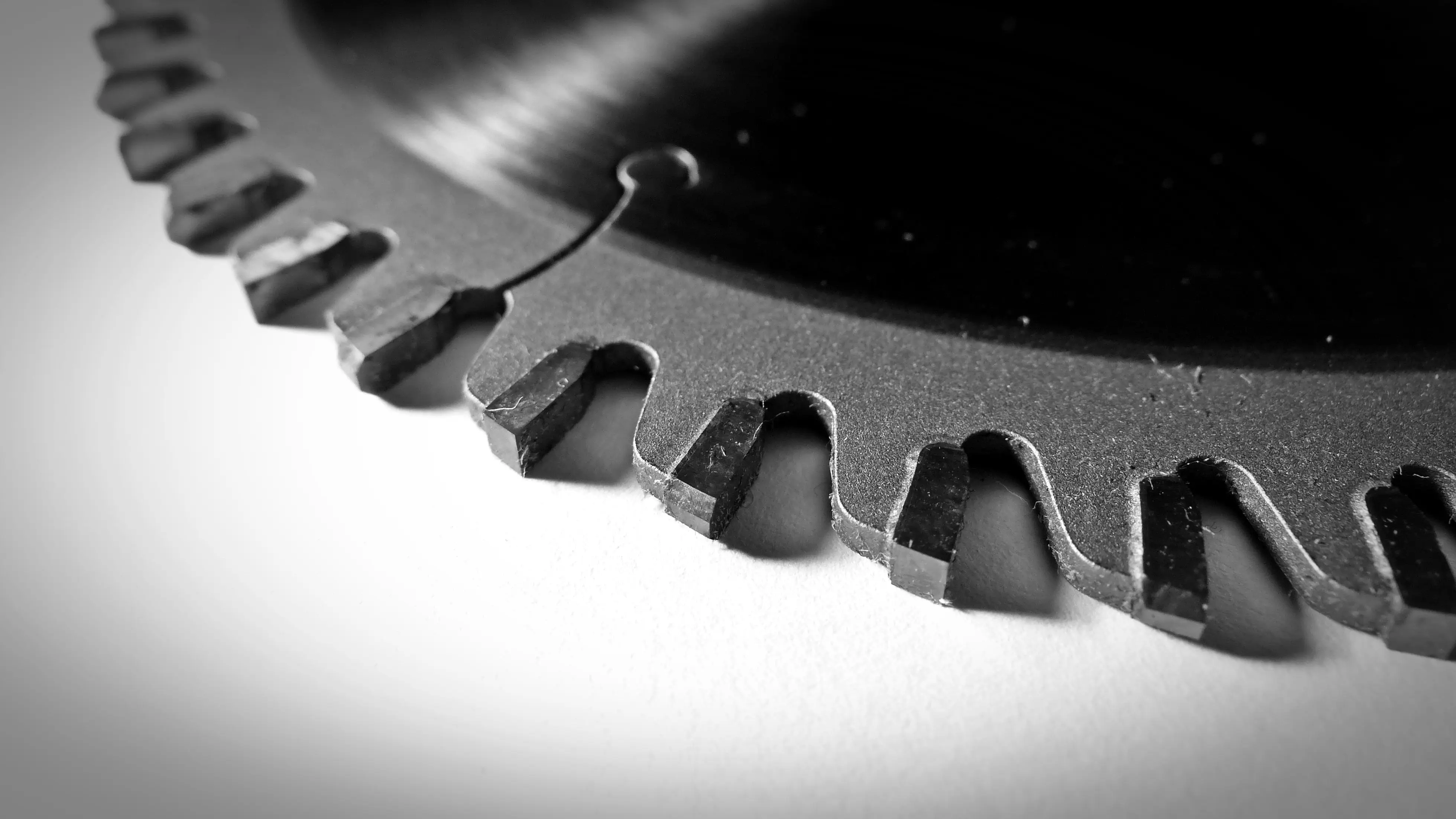
How Induction Heating Supports Metal Tool Manufacturing
Induction heating delivers localized, controllable heat — perfect for targeted hardening, precision brazing, and treating cutting edges or specific tool zones without affecting the entire body. It’s clean, repeatable, and compatible with a wide range of geometries.
Common Induction Heating Applications in the Metal Tooling Industry
- Purpose: Increase surface hardness while preserving core toughness
- Tools:
- Gear cutters
- Chisels, punches
- Screwdrivers, hex keys
- Lathe tools, cutting inserts
- Benefits:
- Targeted hardening of working surfaces or edges
- Consistent hardness depth and profile
- Reduced warping or distortion compared to furnace methods
- Used after hardening to reduce brittleness
- Tools:
- High-speed steel drills
- Impact tools (hammers, dies)
- Benefits:
- Improved toughness
- Customizable mechanical properties
- Process: Softens metal to allow further machining or forming
- Tools:
- Blanks for cold working
- Re-sharpened cutting tools
- Benefits:
- Restores ductility
- Relieves internal stress from forming or welding
- Used to join different materials (e.g., carbide to steel)
- Tools:
- Tipped cutting tools (e.g., carbide inserts on saw blades)
- Reamers and milling tools
- Benefits:
- Strong joints with excellent thermal conductivity
- Minimal heat-affected zone
- Clean and flux-efficient process
- Used for tool and holder assemblies
- Tools:
- Shrink-fit tool holders
- Precision mandrels
- Benefits:
- No mechanical force needed
- Strong, vibration-free fits
- Easy disassembly with reheating
Benefits of Induction Heating in Tool Manufacturing
- Precision control: Essential for critical surfaces and edges
- Reduced energy waste: Heats only the necessary area
- Repeatable results: High consistency for batch production
- Minimal distortion: Maintains tolerances, even on long tools
- Automation-friendly: Suitable for robotic integration
- Environmentally cleaner: No flames or toxic emissions
Free Application Analysis
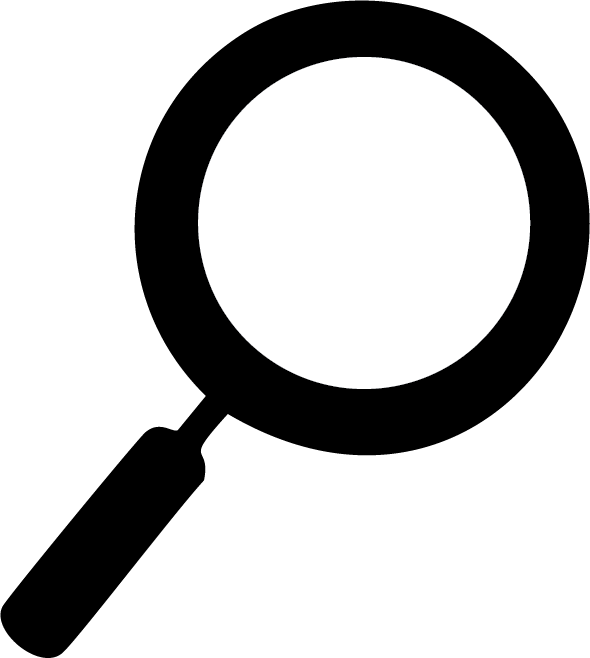
Complimentary sample testing
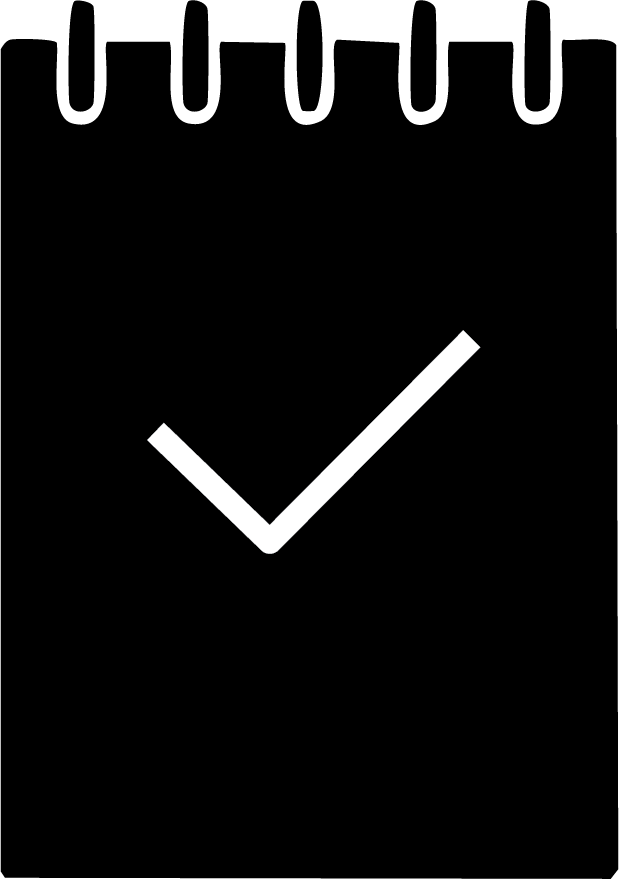
Fast Quotes
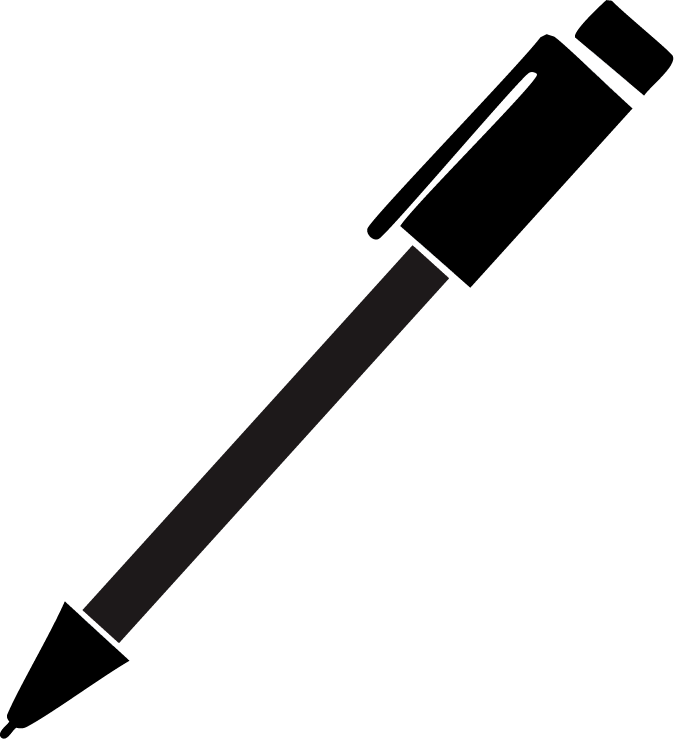