The Aerospace Advantage of Induction Surface Hardening
- Jamie RunevitchInduction surface hardening gives aerospace manufacturers a precise way to boost durability in parts like landing gear and shafts without adding weight or causing distortion. It treats only the surface, improving wear and fatigue resistance while maintaining tight tolerances.
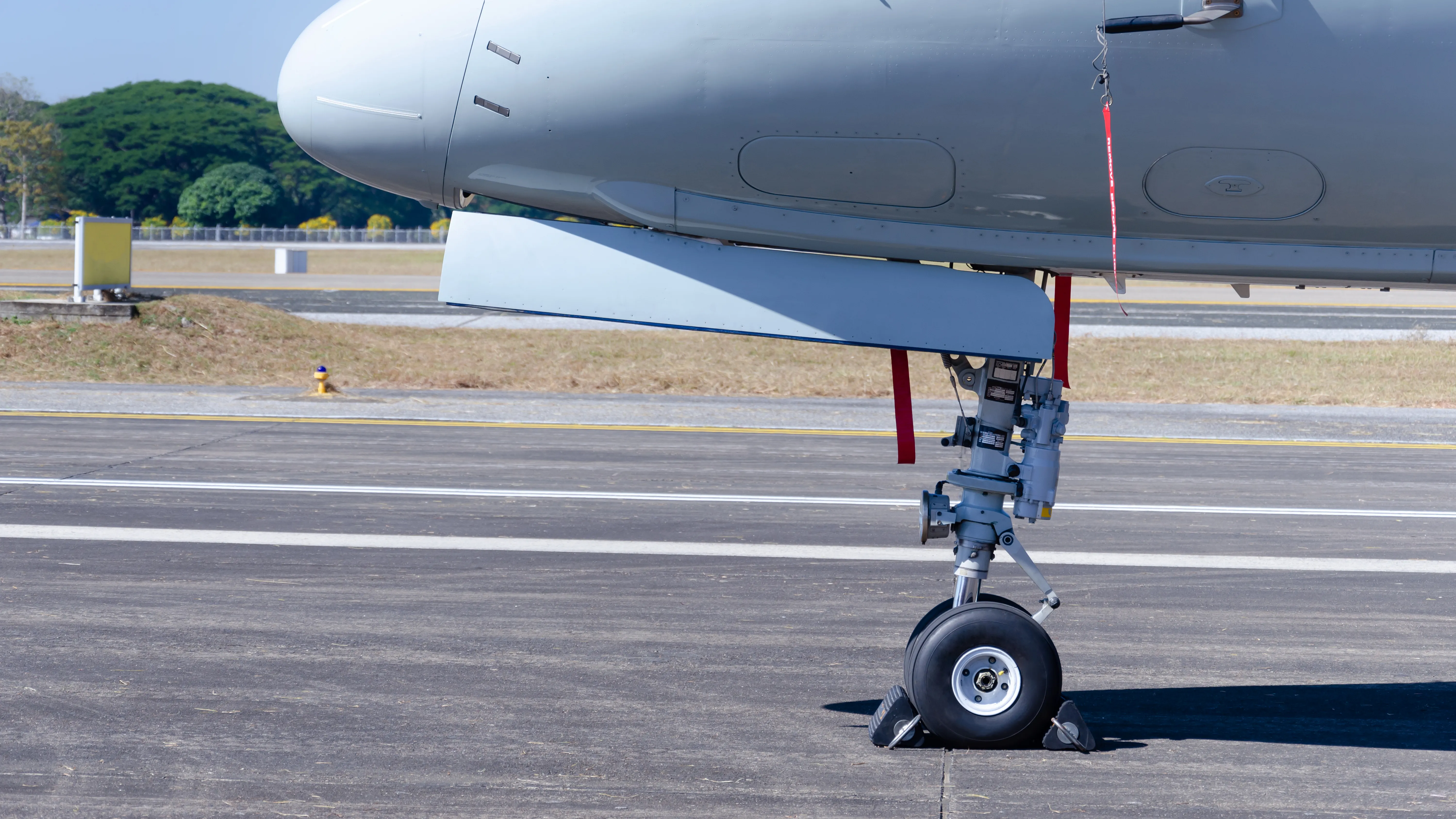
In aerospace engineering, every component must meet extreme demands for strength, reliability, and weight optimization. For high-stress components such as landing gear, transmission shafts, and actuation gears, durability under repeated load cycles is non-negotiable. This is where induction surface hardening offers a critical advantage.
Why Surface Hardening Matters in Aerospace
Aerospace components are subject to high mechanical loads, rapid cycling, and extreme environmental conditions. These factors create intense surface-level wear and fatigue risk. Surface hardening addresses this by creating a hardened outer shell while maintaining a tough, ductile core. The result is a component that resists wear and fatigue cracking while still absorbing shock loads, which is crucial for applications such as landing gear and rotating shafts.
Induction Heating: Built for Aerospace Demands
Induction surface hardening uses controlled electromagnetic fields to heat just the surface layer of a steel component. The process is rapid, contactless, and precise, allowing engineers to harden only the areas that need it without distorting the entire part.
In aerospace applications, this precision means:
- Less post-processing and minimal distortion
- Faster turnaround times than traditional furnace-based treatments
- Higher repeatability, ideal for small-batch, high-spec manufacturing
- Cleaner operations aligned with aerospace sustainability goals
Industries like aerospace have traditionally used carburizing and other furnace methods, but the high level of process control and repeatability offered by induction heating makes it a viable and often superior alternative.
Common Aerospace Applications
Landing Gear Components
Require hardened surfaces to withstand thousands of impact cycles without deformation or wear.
Engine and Gearbox Shafts
Benefit from fatigue-resistant surfaces, improving service life and maintenance intervals.
Actuation Gears and Splines
Precision surface hardening enhances performance under fluctuating loads, especially in control surfaces and flap systems.
Advantages Specific to Aerospace Manufacturing
Localized Heat Treatment
Limits the thermal effect to where it’s needed—ideal for complex or lightweight aerospace components.
Compatibility with Alloy Steels Used in Aerospace
Induction hardening is well suited for materials like AISI 4340 and 300M, commonly used in landing gear and flight systems.
Minimal Distortion for Precision Parts
Aerospace tolerances are tight. Induction heating’s rapid cycle and localized energy reduce the risk of dimensional changes during heat treatment.
As aerospace systems become more complex and performance-focused, manufacturing methods must deliver reliability without compromise. Induction surface hardening offers the strength, precision, and efficiency modern aerospace components require, making it a powerful solution for next-generation aircraft platforms.
Free
Application Analysis
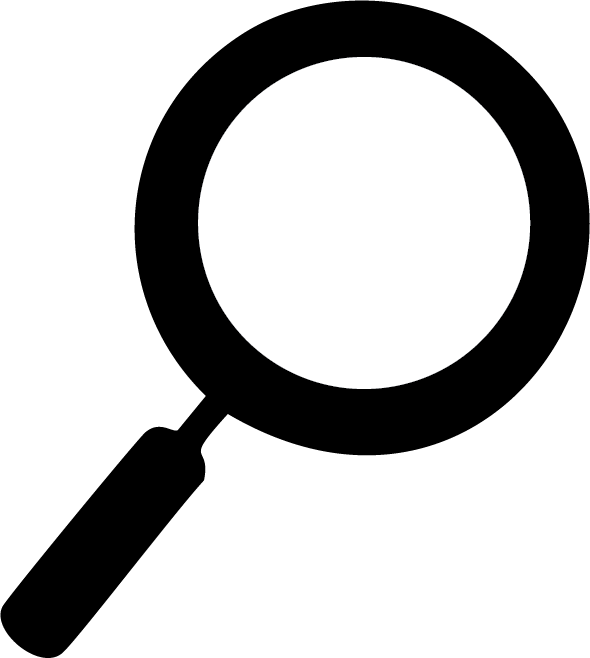
Complimentary
sample testing
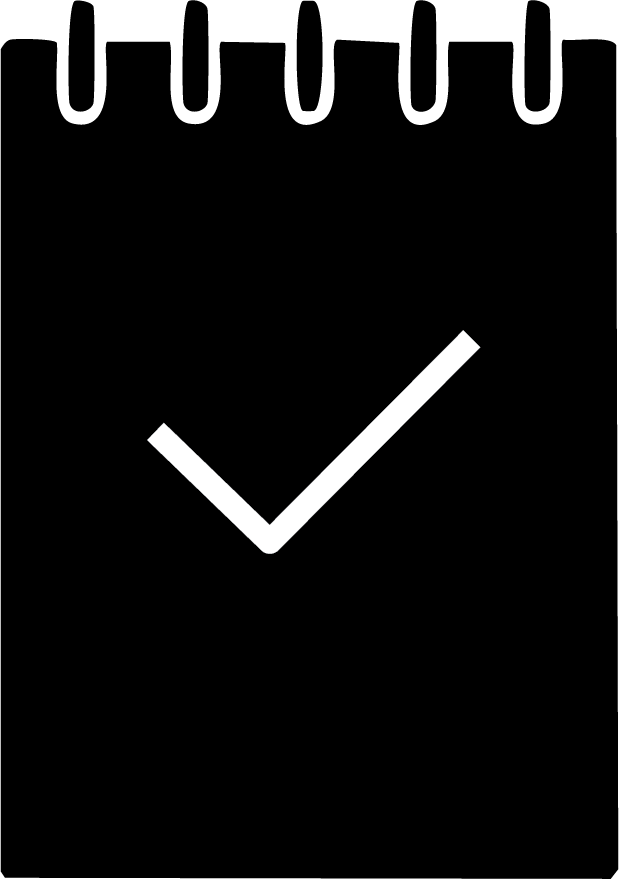
Fast
Quotes
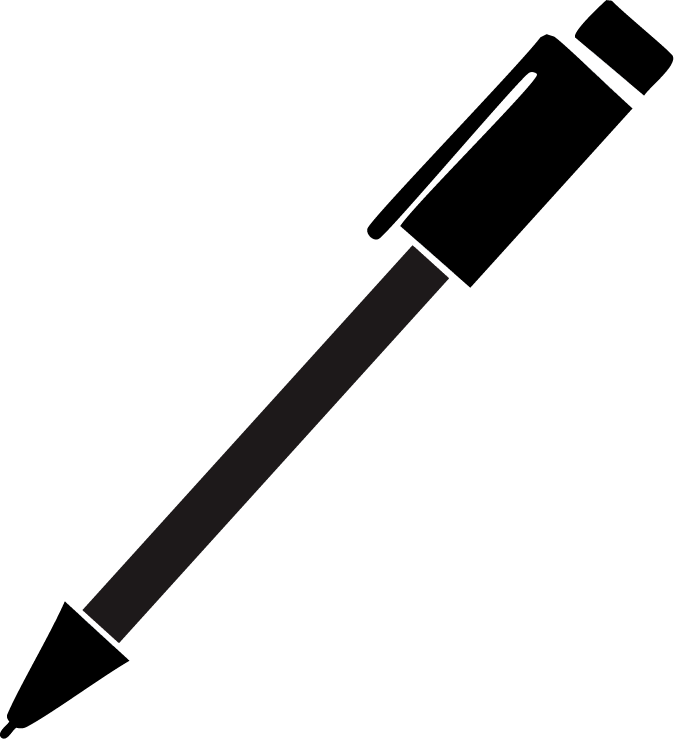