Precision Forging Solutions Powered by Induction Heating
- Jamie RunevitchInduction heating is gaining traction in forging for its speed, precision, and energy savings. It provides targeted, repeatable heat for billets, bar ends, and parts. This blog looks at how it’s helping manufacturers boost productivity and cut costs.
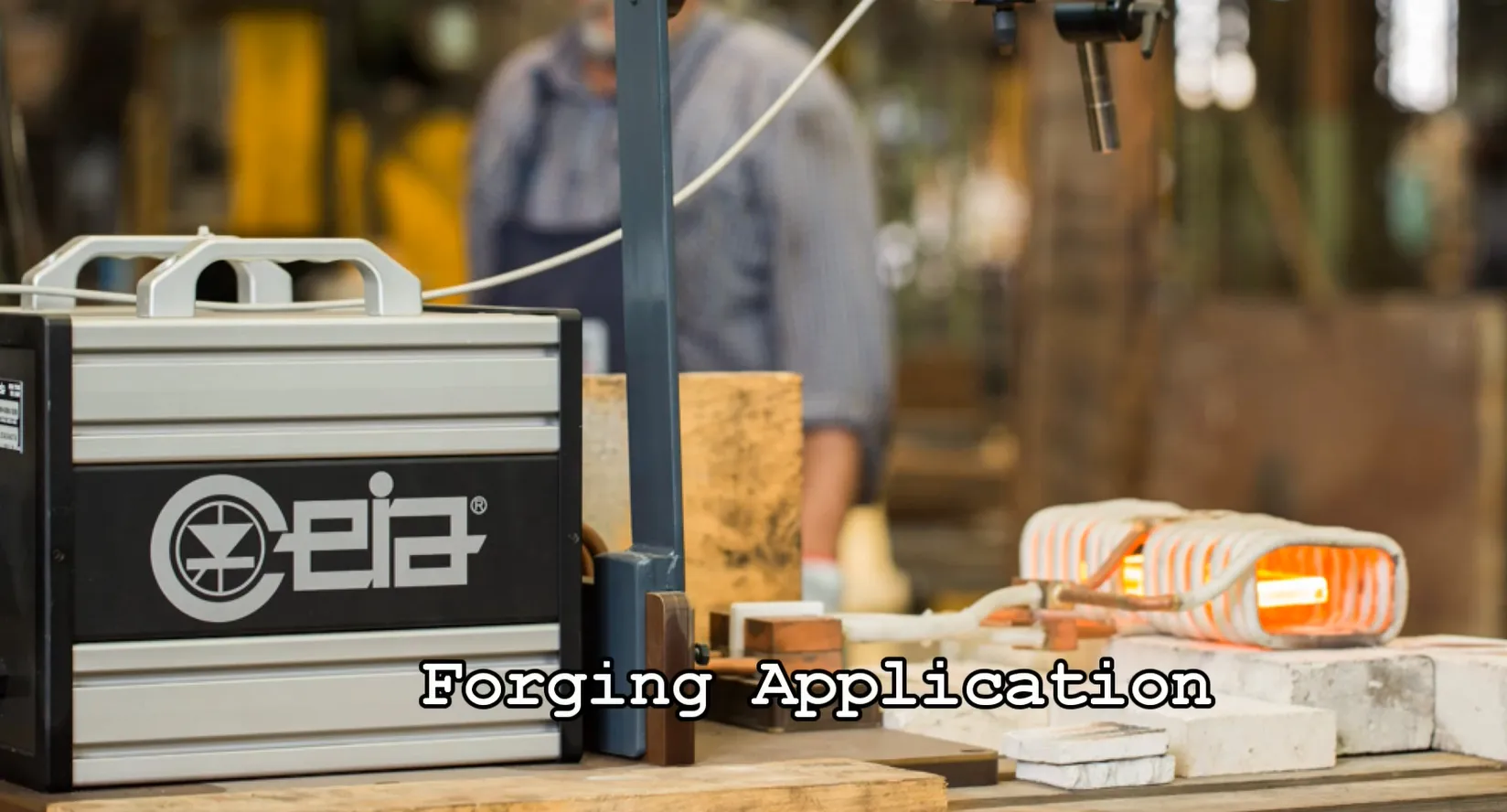
Forging is one of the oldest and most dependable metalworking processes, used to shape metal parts under pressure from hammers or presses. Whether warm or hot forging, each method plays a role in shaping components for critical industries such as automotive, aerospace, and manufacturing.
As the demand for precision, energy savings, and faster cycle times continues to grow, many operations are shifting away from traditional furnace or torch heating. Induction heating has emerged as a more innovative alternative, offering efficient, targeted, and reliable heating that modern forging applications require.
What is Induction Heating for Forging?
Induction heating uses electrical currents to create heat directly within the metal part. The process is non-contact, clean, and capable of delivering heat rapidly to a specific section or the entire part. Whether you're heating a full billet or just the end of a bar, induction offers a level of precision that's difficult to match with conventional methods.
Why Choose Induction Heating for Forging?
When it comes to preparing metal parts for forging, induction heating offers distinct advantages:
- Faster heating: Reaches forging temperatures in moments, reducing production cycle times
- Precision and consistency: Allows for localized or full-part heating with repeatable results
- Energy efficiency: Consumes less energy than gas or resistance heating methods
- Cleaner, safer operation: Eliminates open flames and reduces excess heat in the work environment
- Easily automated: Can be integrated or automated production lines for seamless workflow
Real-World Forging Applications
Induction heating is widely used across industries where speed, precision, and consistency are essential. Below are several examples of how it's applied in real-world forging environments:
Hot Heading Fasteners
- Steel rods are heated in seconds for hot heading, replacing slower and less precise torch systems. This method ensures a uniform heat pattern, improving die life and forging consistency in the fastener industry.
Forming Magnetic Steel Parts
- Components are brought up to forming temperature in just a few minutes using precisely designed coils. This delivers a clean and targeted heat that's safer and more repeatable than flame heating.
Heating Rods of Varying Materials
- Induction can handle steel, stainless steel, titanium, and Inconel rods. A single coil can be designed to accommodate all variations, allowing for flexible production.
Brass Rod Preheating
- In operations where brass cylinders must be heated quickly before forging, induction cuts down cycle times. This not only speeds up production but also creates a more controlled work environment.
Billet Preheating for Rolling or Pressing
- Billets can be preheated to precise surface temperatures before being transferred into a forge press or rolling line. Preheating with induction improves energy efficiency, shortens furnace time, and helps maintain consistent grain structure in the final part.
Preheating Before Secondary Processing
- For certain materials, parts are preheated to moderate temperatures before being introduced into a gas furnace or a secondary operation. This hybrid approach reduces strain on larger heating systems and improves overall throughput.
Through-Curie Heating
- Specialized applications require heating parts past the Curie point to alter magnetic properties or prepare for further metallurgical changes. Induction enables these transitions with fine-tuned temperature control and consistent results.
Flexible Systems for a Range of Needs
Induction systems can be customized for different materials, part sizes, and process speeds. Frequency ranges from as low as 6kHz for large billets up to 100kHz for small, high-speed parts. Whether it's bar end heating for automotive components or billet heating for industrial parts, systems can be tuned to deliver consistent heat without sacrificing productivity.
Test Before You Commit
One of the biggest advantages of induction heating is the ability to test your application before committing to a system. CEIA USA offer free lab testing, where engineers evaluate your parts, determine the optimal heating profile, and provide video proof along with a recommended system setup.
This ensures the solution will meet your specific production goals, whether you're scaling up output, improving energy usage, or eliminating inconsistencies in your current process.
A Modern Solution for Modern Forging
Induction heating represents a leap forward in forging technology. It offers cleaner, faster, and more controlled heating. It's ideal for companies looking to increase efficiency, ensure quality, and stay competitive in today's demanding manufacturing landscape.
Interested in exploring induction heating for your forging process? Start by testing your parts with an applications team and see the results firsthand.
Free Application Analysis
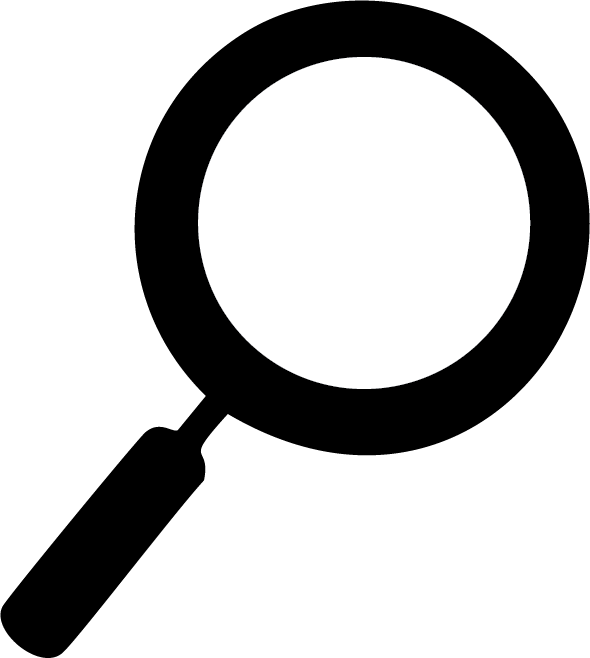
Complimentary sample testing
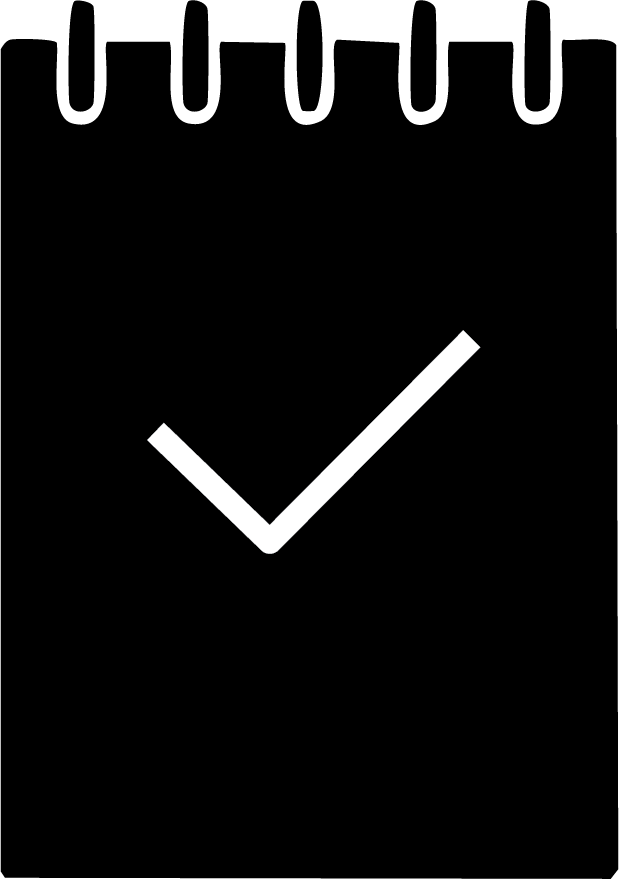
Fast Quotes
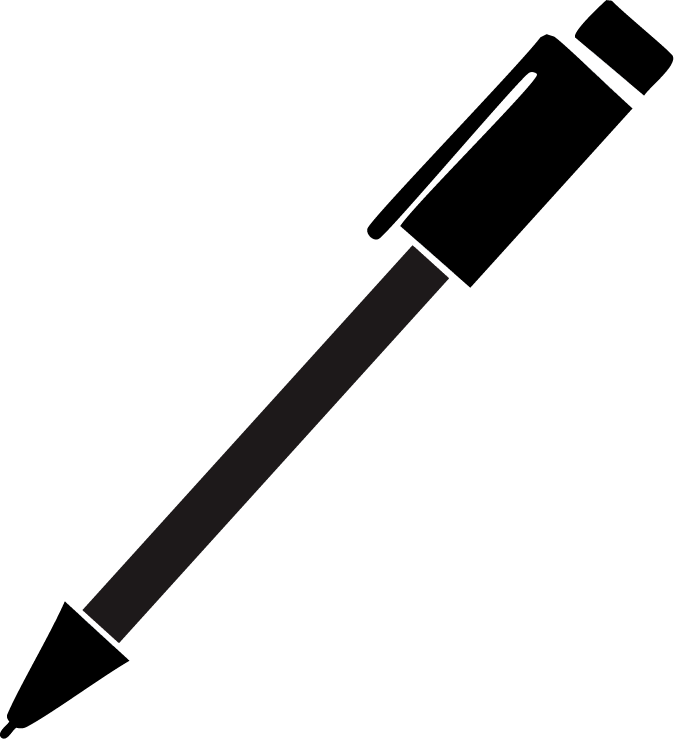